Problem Statement
The automotive industry is undergoing a significant transformation driven by the adoption of 3D printing and other advanced manufacturing techniques. These technologies are reshaping how vehicles are designed, prototyped, and produced, offering unprecedented levels of flexibility, efficiency, and innovation. However, while the benefits are substantial, the industry must also navigate the challenges associated with integrating these technologies into traditional manufacturing processes.
3D printing, or additive manufacturing, enables the creation of complex parts and components that would be difficult or impossible to produce using conventional methods. This capability allows for rapid prototyping, where vehicle designs can be quickly tested, iterated, and refined without the need for expensive and time-consuming tooling changes. As a result, automotive manufacturers can accelerate the development cycle, bringing new models to market faster than ever before.
Customization is another key advantage of 3D printing in the automotive industry. The ability to produce parts on-demand means that manufacturers can offer highly personalized vehicles tailored to individual customer preferences. This level of customization extends beyond aesthetics, allowing for functional modifications that enhance performance, comfort, and safety. As consumer demand for personalized products continues to grow, 3D printing positions manufacturers to meet these expectations more effectively.
In addition to customization, 3D printing also supports on-demand production, reducing the need for large inventories of parts and components. Traditional manufacturing often requires the production of parts in large quantities to achieve economies of scale, leading to excess inventory and increased storage costs. With 3D printing, manufacturers can produce parts as needed, minimizing waste and reducing inventory-related expenses.
Despite these advantages, the integration of 3D printing and advanced manufacturing techniques into the automotive industry is not without its challenges. One of the primary concerns is the scalability of these technologies for mass production. While 3D printing excels in producing small batches of customized parts, scaling up to produce thousands or millions of units at a competitive cost remains a challenge. Manufacturers must explore hybrid approaches that combine additive manufacturing with traditional methods to achieve the necessary scale.
Quality control is another critical issue. Ensuring that 3D-printed parts meet the stringent safety and performance standards required in the automotive industry is essential. This requires the development of new testing and validation protocols specifically tailored to additive manufacturing. Manufacturers must also invest in advanced materials and technologies that enhance the durability and reliability of 3D-printed components.
Furthermore, the adoption of 3D printing and advanced manufacturing techniques necessitates a shift in the workforce. Engineers, designers, and production staff must be trained in these new technologies, requiring investment in education and training programs. Additionally, the integration of digital design and manufacturing processes presents cybersecurity risks that must be addressed to protect intellectual property and ensure the integrity of production systems.
To fully realize the potential of 3D printing in the automotive industry, manufacturers must navigate these challenges while continuing to innovate and push the boundaries of what is possible in vehicle design and production. By doing so, they can achieve significant reductions in lead times, inventory costs, and production waste, while offering customers greater customization and faster access to the vehicles of their dreams.
Pain Points
- Scalability for Mass Production: Challenges in scaling 3D printing technologies to produce large quantities of parts at a competitive cost.
- Quality Control: Ensuring that 3D-printed parts meet stringent safety and performance standards required in the automotive industry.
- Workforce Training: The need for investment in education and training programs to equip engineers, designers, and production staff with the skills required for 3D printing and advanced manufacturing.
- Cybersecurity Risks: Protecting intellectual property and ensuring the integrity of digital design and manufacturing processes from cyber threats.
- Material Advancements: Developing and utilizing advanced materials that enhance the durability and reliability of 3D-printed components.
- Integration with Traditional Manufacturing: Combining 3D printing with conventional manufacturing methods to achieve necessary production scale.
- Supply Chain Adaptation: Adapting supply chains to accommodate on-demand production and reduce reliance on large inventories.
- Cost Management: Balancing the costs of implementing advanced manufacturing technologies with the potential savings in lead times and inventory.
- Environmental Impact: Addressing the environmental implications of 3D printing, including material waste and energy consumption.
- Regulatory Compliance: Navigating the regulatory landscape to ensure that 3D-printed parts comply with industry standards and safety regulations.
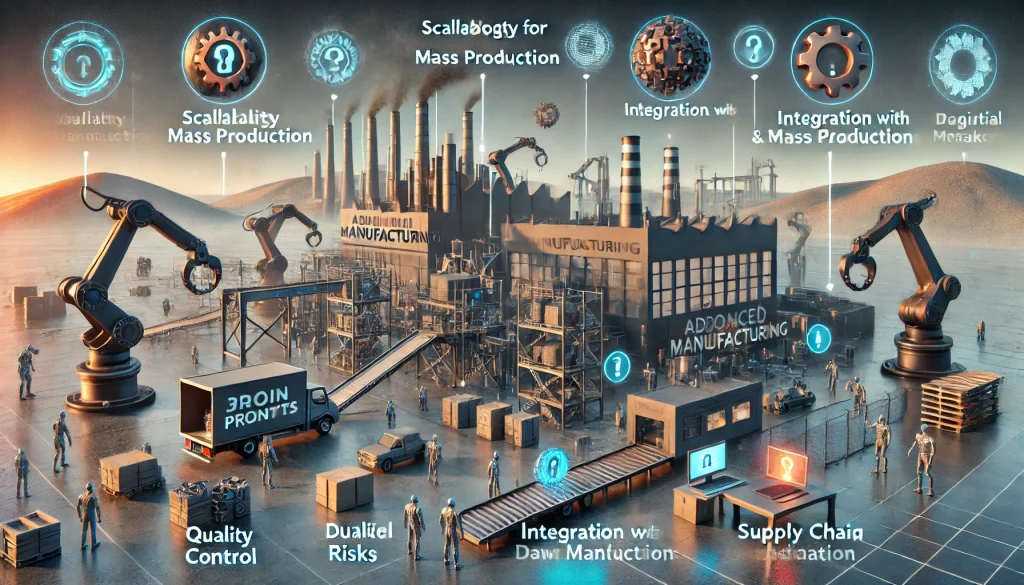
Future Vision
Our platform envisions a future where 3D printing and advanced manufacturing techniques are fully integrated into the automotive industry, revolutionizing how vehicles are designed, produced, and delivered. By leveraging these technologies, automotive manufacturers can achieve unprecedented levels of customization, efficiency, and sustainability while maintaining the highest standards of quality and safety.
Scalability for mass production will be a key focus of the platform. We will support manufacturers in exploring hybrid production models that combine the strengths of 3D printing with traditional manufacturing techniques. This approach will enable the efficient production of both customized and standardized parts, allowing manufacturers to scale up production without compromising on cost or quality.
Quality control will be enhanced through the development of advanced testing and validation protocols specifically designed for 3D-printed components. The platform will provide tools and resources to ensure that all parts meet or exceed the safety and performance standards required in the automotive industry. Additionally, ongoing research and development of advanced materials will further improve the durability and reliability of 3D-printed parts, making them suitable for a wide range of applications.
Workforce training will be prioritized, with the platform offering comprehensive education and training programs for engineers, designers, and production staff. These programs will equip the workforce with the skills needed to operate and innovate in an environment where 3D printing and advanced manufacturing are central to the production process. By investing in talent development, manufacturers can ensure a smooth transition to these new technologies and maintain a competitive edge in the market.
Cybersecurity will also be a critical component of the platform’s strategy. As digital design and manufacturing processes become more prevalent, protecting intellectual property and ensuring the integrity of production systems will be paramount. The platform will provide cybersecurity solutions tailored to the needs of the automotive industry, helping manufacturers safeguard their innovations and maintain the trust of their customers.
Environmental sustainability will be integrated into the platform’s vision. By promoting on-demand production and reducing reliance on large inventories, manufacturers can minimize waste and lower their environmental footprint. The platform will also support the development of eco-friendly materials and energy-efficient production methods, aligning with the industry’s broader goals of sustainability and corporate responsibility.
Through these strategies, the platform will enable automotive manufacturers to fully realize the potential of 3D printing and advanced manufacturing, driving innovation and transforming the way vehicles are designed, produced, and delivered.
Use Cases
- Hybrid Production Models: Implementing hybrid models that combine 3D printing with traditional manufacturing techniques to achieve scalable production.
- Advanced Quality Control Protocols: Developing testing and validation protocols specifically designed for 3D-printed automotive components.
- Workforce Education and Training: Offering comprehensive training programs to equip engineers, designers, and production staff with the skills required for 3D printing and advanced manufacturing.
- Cybersecurity Solutions: Providing tailored cybersecurity solutions to protect intellectual property and ensure the integrity of digital manufacturing processes.
- Advanced Material Development: Researching and developing new materials that enhance the durability, reliability, and sustainability of 3D-printed automotive parts.
- On-Demand Production: Facilitating on-demand production to reduce inventory costs and waste while enabling greater customization for customers.
- Cost-Efficiency Analysis: Conducting cost-efficiency analyses to balance the costs of implementing advanced manufacturing technologies with potential savings.
- Environmental Sustainability Initiatives: Promoting eco-friendly materials and energy-efficient production methods to minimize the environmental impact of 3D printing.
- Regulatory Compliance Tools: Providing tools and resources to help manufacturers navigate the regulatory landscape and ensure compliance with industry standards.
- Customer-Centric Customization: Leveraging 3D printing to offer highly personalized vehicles tailored to individual customer preferences and needs.
Target Users and Stakeholders
- User: Automotive Manufacturers, Engineers, Designers, Production Managers, Cybersecurity Teams, and Compliance Officers
- Age Group: 30-60 years
- Gender: M/F
- Usage Pattern: Regular usage for integrating 3D printing and advanced manufacturing techniques into vehicle design and production processes
- Benefit: Enhanced ability to innovate, reduce lead times and inventory costs, and offer greater customization while maintaining high standards of quality and safety
- Stakeholders:
- Automotive Manufacturers: Companies involved in the design, production, and delivery of vehicles, seeking to innovate and improve efficiency through advanced manufacturing techniques.
- Suppliers: Providers of materials and components used in 3D printing and traditional manufacturing, playing a critical role in the supply chain.
- Customers: Individuals and businesses seeking customized vehicles with advanced features, faster delivery times, and higher quality.
- Regulatory Bodies: Agencies responsible for setting and enforcing safety, environmental, and quality standards in the automotive industry.
- Technology Providers: Companies offering 3D printing equipment, software, materials, and cybersecurity solutions tailored to the automotive sector.
Key Competition
- Ford: Leveraging 3D printing for prototyping and producing customized components, reducing lead times and enabling greater innovation in vehicle design.
- General Motors: Investing in additive manufacturing to create lightweight, durable parts and enhance the efficiency of vehicle production.
- BMW: Utilizing 3D printing to produce complex, customized components, supporting both prototyping and small-scale production.
- Tesla: Incorporating advanced manufacturing techniques, including 3D printing, to accelerate product development and enhance vehicle performance.
- Volkswagen: Implementing 3D printing technologies to streamline production processes and reduce costs associated with prototyping and part production.
Products/Services
- Ford 3D Prototyping Solutions: Leveraging 3D printing for rapid prototyping and customized component production, reducing lead times and enabling greater innovation.
- GM Additive Manufacturing: Creating lightweight, durable parts through additive manufacturing, enhancing the efficiency of vehicle production.
- BMW Customization: Utilizing 3D printing to produce complex, customized components for both prototyping and small-scale production.
- Tesla Advanced Manufacturing: Incorporating 3D printing and other advanced techniques to accelerate product development and enhance vehicle performance.
- Volkswagen Production Streamlining: Implementing 3D printing technologies to streamline production processes and reduce prototyping and part production costs.
Active Startups
- AutoPrint: Specializes in 3D printing solutions for the automotive industry, focusing on rapid prototyping and customized component production.
- ProtoFlex: Offers flexible 3D printing services that enable automotive manufacturers to quickly iterate on designs and reduce time-to-market.
- SecureAuto: Provides cybersecurity solutions tailored to the needs of automotive manufacturers using digital design and manufacturing processes.
- EcoParts: Focuses on developing eco-friendly materials for 3D printing in the automotive industry, promoting sustainability and reducing environmental impact.
- OnDemandAuto: Specializes in on-demand production services, enabling automotive manufacturers to reduce inventory costs and offer greater customization.
- ScalePrint: Develops scalable 3D printing technologies that allow for the efficient production of large quantities of automotive components.
- AutoMaterial: Innovates in the development of advanced materials for 3D-printed automotive parts, enhancing durability and reliability.
- RegComplyAuto: Provides regulatory compliance tools and resources for automotive manufacturers using 3D printing and advanced manufacturing techniques.
- AutoDesignLab: Offers design and prototyping services that leverage 3D printing to create highly customized and innovative vehicle components.
- AutoCyberGuard: Specializes in protecting intellectual property and securing digital manufacturing processes in the automotive industry.
Ongoing Work in Related Areas
- Hybrid Production Research: Exploring the integration of 3D printing with traditional manufacturing techniques to achieve scalable production in the automotive industry.
- Advanced Material Development: Innovating in the development of new materials that enhance the durability, reliability, and sustainability of 3D-printed automotive parts.
- Workforce Training and Education: Developing comprehensive training programs to equip engineers, designers, and production staff with the skills needed for 3D printing and advanced manufacturing.
- Cybersecurity in Digital Manufacturing: Researching and developing cybersecurity solutions tailored to the needs of automotive manufacturers using digital design and manufacturing processes.
- Environmental Impact Studies: Conducting studies to assess and reduce the environmental impact of 3D printing and advanced manufacturing in the automotive industry.
- Regulatory Compliance Innovations: Innovating tools and resources to help automotive manufacturers navigate the regulatory landscape and ensure compliance with industry standards.
- Cost Efficiency in Advanced Manufacturing: Exploring strategies for balancing the costs of implementing advanced manufacturing technologies with potential savings in lead times and inventory.
- On-Demand Production Techniques: Developing new techniques for on-demand production, enabling automotive manufacturers to reduce inventory costs and offer greater customization.
- Customer-Centric Vehicle Design: Innovating in the design and production of highly personalized vehicles that meet individual customer preferences and needs.
- Supply Chain Adaptation: Researching strategies for adapting supply chains to accommodate on-demand production and reduce reliance on large inventories.
Recent Investment
- AutoPrint: $50M in Series B funding led by automotive technology-focused venture capital firms, March 2021.
- ProtoFlex: $40M in Seed funding from rapid prototyping and advanced manufacturing investors, May 2020.
- SecureAuto: $35M in Series A funding from cybersecurity-focused investment firms, August 2021.
- EcoParts: $30M in Series A funding from sustainability and automotive investors, October 2020.
- OnDemandAuto: $25M in Seed funding from on-demand production and automotive technology investors, December 2020.
Market Maturity
The market for 3D printing and advanced manufacturing solutions in the automotive industry is rapidly maturing as manufacturers recognize the transformative potential of these technologies. Companies like Ford, GM, and Tesla are leading the way with innovative applications of 3D printing for prototyping, customization, and part production. Startups such as AutoPrint, ProtoFlex, and SecureAuto are driving innovation in rapid prototyping, scalable production, and cybersecurity for digital manufacturing. Significant investments in hybrid production research, advanced material development, and on-demand production techniques are reshaping the automotive industry, enabling manufacturers to reduce lead times, inventory costs, and production waste while offering greater customization and faster access to vehicles. As the market continues to evolve, we expect to see more integrated and advanced solutions that enhance the efficiency, sustainability, and innovation of vehicle design and production.
Summary
The adoption of 3D printing and other advanced manufacturing techniques is transforming how vehicles are designed and produced. These technologies allow for rapid prototyping, customization, and on-demand production, reducing lead times and inventory costs. However, challenges such as scalability for mass production, quality control, workforce training, cybersecurity risks, material advancements, integration with traditional manufacturing, supply chain adaptation, cost management, environmental impact, and regulatory compliance must be addressed. Our proposed platform leverages hybrid production models, advanced quality control protocols, workforce education and training, cybersecurity solutions, advanced material development, on-demand production, cost-efficiency analysis, environmental sustainability initiatives, regulatory compliance tools, and customer-centric customization to address these challenges.
Target users include automotive manufacturers, engineers, designers, production managers, cybersecurity teams, and compliance officers, with stakeholders encompassing automotive manufacturers, suppliers, customers, regulatory bodies, and technology providers. Key competitors like Ford, GM, BMW, Tesla, and Volkswagen offer various 3D prototyping solutions, additive manufacturing technologies, customization options, and advanced manufacturing techniques, while startups such as AutoPrint, ProtoFlex, and SecureAuto are driving innovation in rapid prototyping, scalable production, and cybersecurity for digital manufacturing. Recent investments highlight significant interest and growth potential in platforms addressing the challenges of 3D printing and advanced manufacturing in the automotive industry.
By addressing these challenges and implementing innovative 3D printing and advanced manufacturing strategies, automotive manufacturers can revolutionize vehicle design and production, driving innovation and transforming the industry.